Benchtop Lathe
Project Overview
Objective: Build a working benchtop lathe capable of machining aluminum and surviving the "Death Test"
Role: Designed & Manufactured the following subsystems: motor mount assembly, drivetrain, rail carriage & support, lead screw fixture ("Dancing Man")
Skills: CAD modeling, FEA (static load, drop test, fundamental frequencies), waterjet, endmill, jig design, bearings (life, preload, etc.)
Result: Survived the "Death Test" and placed second in the end of semester machining competition
Project Description
This undergraduate mechanical engineer course was titled elements of mechanical design. It's an advanced course on modeling, design, integration and best practices for use of machine elements such as bearings, springs, gears, cams and mechanisms. Modeling and analysis of these elements is based upon extensive application of physics, mathematics and core mechanical engineering principles (solid mechanics, fluid mechanics, manufacturing, estimation, computer simulation, etc.). These principles are reinforced via (1) hands-on laboratory experiences wherein students conduct experiments and disassemble machines and (2) a substantial design project wherein students model, design, fabricate and characterize a mechanical system that is relevant to a real-world application (a desktop lathe). Student assessment is based upon mastery of the course materials and the student's ability to synthesize, model and fabricate a mechanical device subject to engineering constraints (e.g., cost and time/schedule).
Students work in teams of 4-5 to fabricate a working desktop lathe capable of machining aluminum bar stock. Certain components are provided in advance such as the spindle and bearings; however, some of these are intentionally designed to fail so students must validate all durability calculations to identify these in advance and swap them out for the lathe to work correctly. Other components, such as the carriage, have the base casting provided but need to be machined to work correctly. However, the majority of components, such as the cross-slide flexure and motor mount, need to be designed and manufactured from scratch. At the end of the semester, students compete to see who can machine their bar stock of aluminum to spec the fastest (machining a certain length, diameter, surface finish, uniformity, etc.). Every lathe must also survive a "Death Test" where the professor drops the lathe from waist height and hammers on the spindle with a sledgehammer. To pass, the lathe must be fully intact and functional after both of these tests.
Please click through the gallery below to learn more about the project. Hovering over an image/video will provide a brief summary of what you're looking at and clicking on it provide a more detailed description.
Photo Gallery & Details

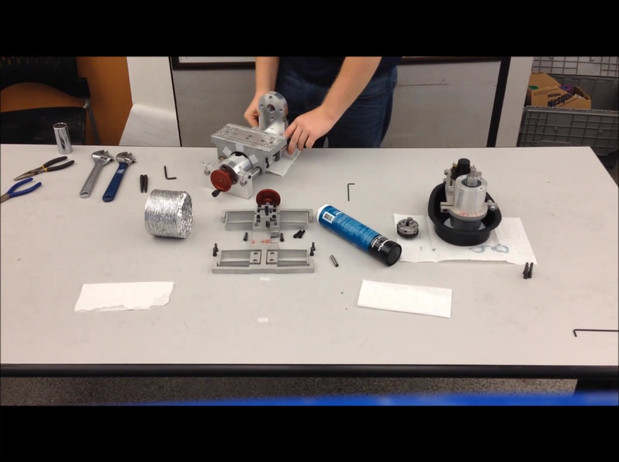


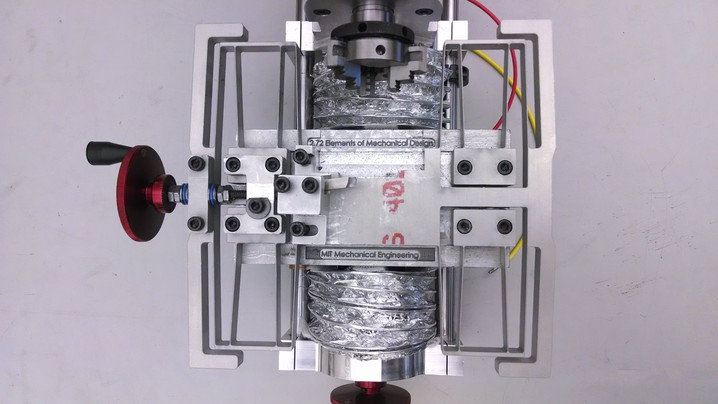


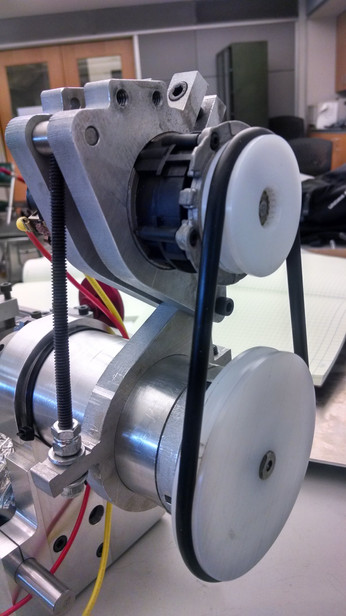
